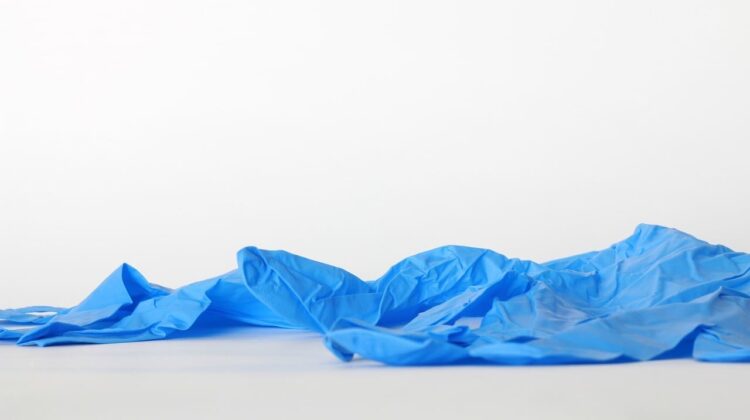
The revolutionary era of self-healing rubber gloves
In the quest for sustainability, “self-healing” rubber gloves is one innovation addressing crucial environmental concerns.
Pioneering the development of the “glove of the future” is the Colloids and Polymer Group, led by Dr Patrick Tang Siah Ying, from the School of Engineering at Monash University, Malaysia.
The team’s work involves infusing cutting-edge materials and self-repairing mechanisms into the polymer matrix of rubber gloves to endure wear and tear more effectively. The autonomous repair mechanism swiftly addresses minor damage, preventing it from escalating.
Dr Tang and his Monash colleagues, research fellow Dr Janarthanan Supramaniam and PhD candidate Darren Low Yi Sern, have long been engaged in researching self-healing rubber technologies.
The team encountered hurdles unique to advanced functional materials during the proof-of-concept stage. Overcoming these challenges required numerous trials, experimenting with various compounding chemical recipes and fabrication methods to demonstrate the material’s self-healing capabilities.
Ensuring a steady supply of resources posed logistical challenges, with key chemicals sourced from speciality vendors and the rubber industry.
“It took a couple of years to understand the science behind self-healing technology, and working with rubber latex of natural and synthetic origins,” Dr Tang says.
“There were also numerous trials with compounding chemicals commonly used in the rubber industry, and how these chemicals could be compatible with the equipment in the laboratories.
“With the successful proof-of-concept for synthetic self-healing rubber achieved in January 2023, the current stage of development involves optimising crucial healing parameters, such as temperature and time, to encourage better healing efficiency.
“Continuous improvement and testing ensure the validity of the formulation, with upcoming stages focusing on technology transfer to create functional glove prototypes bearing these unique self-healing properties.”
Benefits to industry
Self-healing technology is receiving significant attention for the benefits it could bring to the manufacturing industry and users alike, such as better product durability.
When conducting scholarly literature reviews, the research team found most reported materials could self-heal but still lacked strength.
This was due to the need to balance a mobile yet strongly cross-linked network within the material matrix without compromising either side.
Incorporating self-healing technology in rubber gloves exploits the advantage of attractive ionic charges in functionalised fillers and effective compounding agents.
“It was surprising that the strength of our self-healing rubber material surpasses those reported in literature by at least double after healing, compared to an equivalent rubber system,” Dr Tang says.
The material incorporated into the rubber matrix in developing the self-healing gloves was a sustainable nanocellulose filler with relevant functional groups to promote self-healing.
Manipulating the effective functional groups on the surface of the nanocellulose fillers encourages ionic bonding with the rubber chains and their associated compounding constituents, which are reversible and dynamic.
The choice of nanocellulose fillers in the fabrication recipe of the material was made with the primary goal of substituting conventional fillers such as carbon black, silica, mica, and talc.
These conventional fillers have a more significant environmental impact and have, in recent years, been opposed by rubber technologists in formulating more sustainable rubber systems.
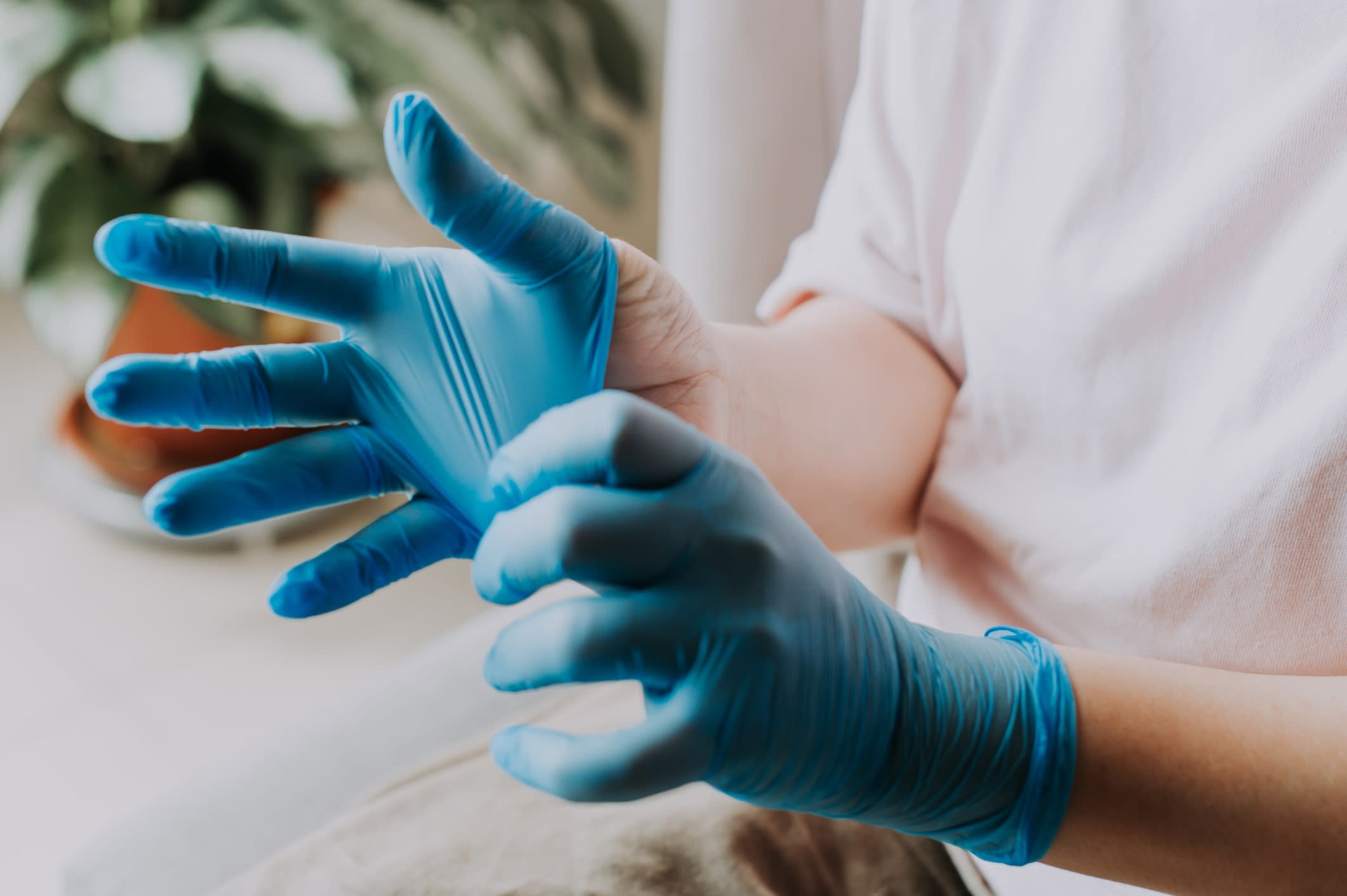
The suitability of nanocellulose
The choice of nanocellulosic fillers is sourced from renewable sources, such as plants, tree parts, and biomass.
Nanocellulose represents the best candidate for reinforcing applications in rubber matrices due to its naturally high strength, tunability, high aspect ratio, and low environmental footprint.
The sustainability value extends beyond rubber processing, where it was also researched that the inclusion of nanocellulose promotes the biodegradability of the rubber glove at the end of its service life.
“It was surprising that the strength of our self-healing rubber material surpasses those reported in literature by at least double after healing, compared to an equivalent rubber system.”
The applications of self-healing rubber gloves span a diverse array of industries, from manufacturing to households.
Whether used in laboratories or industrial settings, these gloves provide a reliable and eco-friendly solution for individuals and businesses keen on minimising their environmental footprint.
In a world collectively striving for sustainability, innovations such as self-healing rubber gloves play a role in reshaping our daily practices.
“Since this is the first of its kind and patented technology, the self-healing rubber glove is yet to be commercialised,” Dr Tang says.
“The viability of pilot-scale production is in the research and development stage. The product has received interest from local and international players within the glove manufacturing industry.
“The user’s overall satisfaction will be determined when the product is produced at a pilot scale, with necessary ethics approval for a direct human trial.”
Glove market to grow
The international industrial glove market is poised for robust growth due to increasing awareness of the significance of personal protective equipment in the workplace.
High-risk industries such as mining, construction, automotive, agriculture, oil and gas, power, solid waste, wastewater treatment, chemical manufacturing, and disposal are driving the market’s expansion as they prioritise user protection.
Beyond offering enhanced protection, self-healing rubber gloves significantly contribute to the reduction of waste, resource consumption, and overall environmental impact.
This article was first published on Monash Lens. Read the original article